Project Profile
AIM Strategy Reduces FPSO Maintenance Backlog 40%
Learn how an optimized Asset Integrity Management (AIM) plan improved critical maintenance activities for an offshore operating company.
Project Objectives
#1
Identify and assess criticality of all equipment onboard the FPSO
#2
Review the client's existing maintenance program and identify opportunities for increased efficiency
#3
Develop and implement an overarching AIM program specific to the client's equipment, operating needs and applications
#4
Evaluate the computerized maintenance management system (CMMS) and prepare client for a future CMMS upgrade
#5
Improve ongoing maintenance efficiency and reduce work order backlog
Project Overview
Due to the demanding offshore environment and the complexity and volume of equipment onboard its FPSO fleet, an operating company frequently battled overloaded maintenance backlogs. The client needed to confirm that the equipment onboard the FPSOs operated at the highest levels of efficiency while downtime was minimized and the operations were completed in a safe, compliant and responsible manner.
To address these client needs, ABS Group's Asset Management and Offshore teams developed and implemented a holistic solution for managing asset integrity and integrating the FPSO systems with processes and best practices to provide maximum asset reliability at the most cost efficient and effective levels.
Client Needs
- Avoid downtime and loss of operational efficiency while maintaining the asset
- Verify that the FPSO fleet maintains adequate safety and integrity standards
- Rank and prioritize critical components onboard the asset
Our Solution
Conduct Equipment Audit and Ranking
To gain a detailed understanding of the mechanical components onboard the client's FPSO, we assisted the owners in identifying each piece of equipment and developing a Master Asset List. After carefully evaluating each system and subsystem, we developed a comprehensive Asset Criticality Ranking (ACR) to identify specific maintenance approaches for each asset based on operational and safety criteria.
Identify Maintenance Approach and Management Process
Using a Risk Based Inspection (RBI) approach, we defined the extent and frequency of maintenance needed for each piece of equipment. The specific needs, usage metrics and exposure of each asset drove these recommendations. We blended this RBI approach with a preventative maintenance program to form a complete mechanical integrity plan.
Additionally, we conducted a review and cleanup of the client's computerized maintenance management system (CMMS) data. To manage ongoing scheduling and maintenance frequency, we input new maintenance schemes and updated process flows in the CMMS.
Ongoing Analysis
As an extension of our reliability engineering program, we provide reliability analytics for the client and conduct structured root cause failure analysis in case of a critical event.
Value Delivered
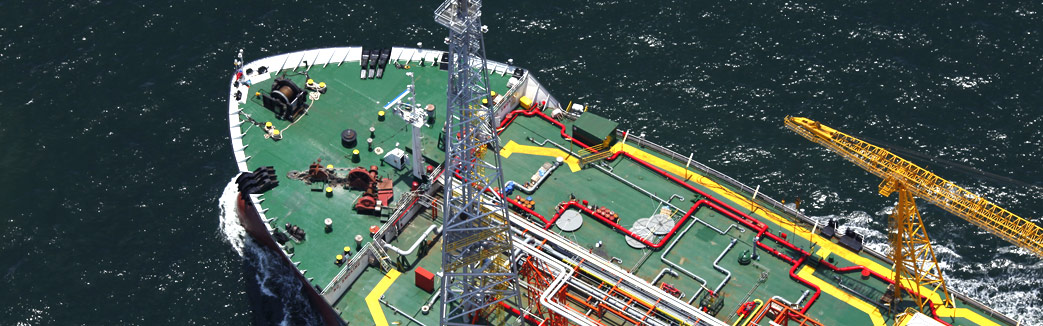
By identifying the specific maintenance needs of the equipment and eliminating unnecessary or overscheduled maintenance, we created a 40% reduction in the work order backlog. This has helped maintenance personnel prioritize and complete critical maintenance projects more quickly and without interference from standard scheduled maintenance tasks.
Additionally, our engineering team reviewed and made improvements to more than 20% of the client's critical system maintenance plans. These improvements promote the strategic allocation of time and resources toward key pieces of equipment and minimize unnecessary maintenance on less critical or lower value assets.
As a result of our efficient condition-based and predictive approach for asset integrity management, future maintenance will incorporate less intrusive inspection techniques, avoiding destructive activity or excessive downtime.