Insight
What Condition is Your Condition Monitoring Program In?
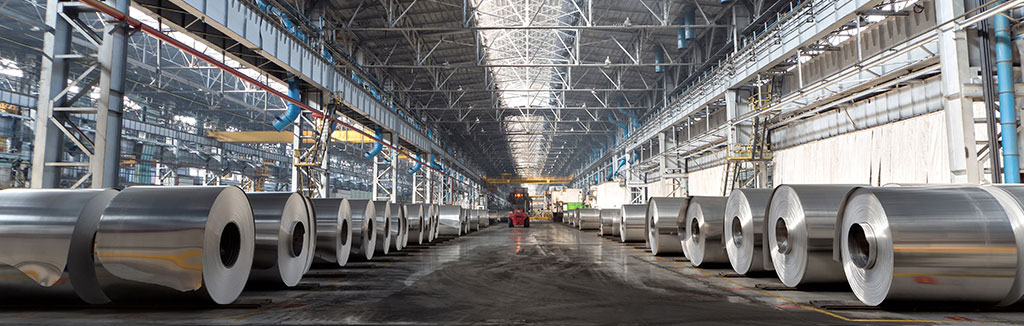
Here's how you create a culture where condition monitoring flourishes.
Condition monitoring (CM) is the backbone of any proactively maintained enterprise asset management program. How else can you and your team members ward off operational deficiencies and failures without knowing what shape your capital-intensive assets are in? How will you know when to respond to those metrics without real-time awareness? Better yet, how will you know when a response is unnecessary and undermining optimal preventive maintenance spend?
Highly effective CM cultures, however, take diligence, coordination, follow-through and proper resourcing - all things that require a consolidated effort from operators,
1. Manage your expectations
Don't expect miracles from your CM
We're not telling you that to crush your dreams of the world of operational excellence that lies ahead. This grounding of sorts serves two strengthening purposes: First, it allows you to be comfortable with small victories instead of striving fruitlessly toward impossible feats. Robust, mature CM programs are built incrementally over many years.
Second, once you understand the limitations of what your sensor tech can do, you can assign them fixed places on asset-specific P-F curves, which chart the potential for equipment degradation over time. Plotting CM sensors according to asset failure trajectories gives asset stakeholders a basic idea of how quickly they must react to adverse readings.
2. Cultivate leadership where it matters most
Cultures of condition monitoring may initiate with an executive decision to invest in more proactive asset management processes, but the benefits of CM emerge only once operators and technicians take matters into their own hands.
But it takes more than a request from a supervisor to establish team buy-in. Facilities must demonstrate the value of the program to staff members in hard numbers, and provide comprehensive training. Balanced support is crucial. Leaders must articulate the importance of using CM tools, while not reprimanding workers should they make mistakes as they learn.
Remember, your operators and technicians are more likely to carry out CM procedures by the books if they have a sturdy foundation to work from and a personal connection with what they're doing.
3. Split your RCA process in two
Root cause analysis (RCA) uncovers the true catalyst buried deep in compromised equipment or resulting from less-than-optimal asset management strategies. In facilities with strong
Immediate RCA focuses on minor emergent deficiencies happening presently and prevents remediators from mistakenly correcting the symptoms of that deficiency instead of the real source. Long-term RCA, on the other hand, looks at the broader responsive strategy as it pertains to outright equipment failures. It asks, What can we do to change how we manage our assets to prevent X failure mode from occurring again?
Many do not differentiate between the pair or perform only one. Both sides of RCA require representation if CM is to give industrial businesses what they want: an in-the-moment, all-encompassing understanding of asset performance and ancillary maintenance processes that guides actionable decision-making.
Real-time asset health assessments through condition monitoring have worked wonders for businesses looking to prolong the life of their critical machinery and reduce operations and maintenance costs, but it takes more than wishful thinking to get a CM program up and running.
Read more about condition monitoring and other core elements of enterprise asset management in our Knowledge Center.