Insight
Ten Keys to an Effective Root Cause Analysis Program
ABS Group Incident Investigation and Root Cause Analysis Services
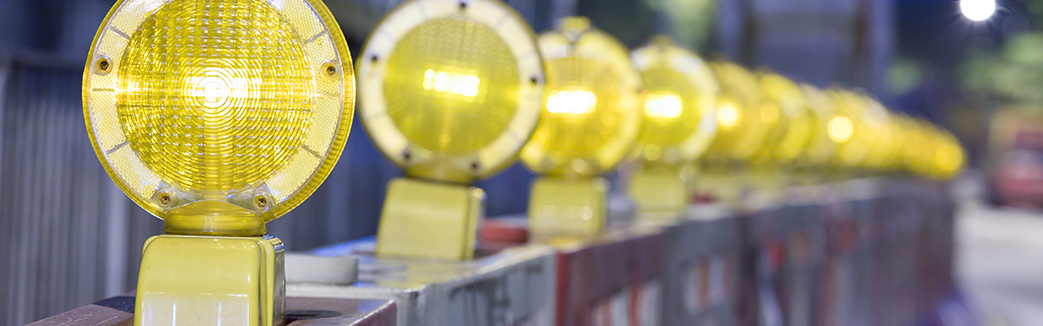
Many organizations struggle with implementation of an effective root cause analysis (RCA) program. In working with hundreds of organizations to develop and implement RCA programs, we have noted a few common threads that seem to emerge regardless of the business type or size.
10 Keys for RCA
1. Think long term
Most organizations focus on the short-term due to immediate financial pressures and the push to resume production. However, this near-sighted focus fosters a "patch it" mentality with no fundamental understanding of the underlying causes. Certainly short-term performance cannot be ignored, but insufficient attention to long-term fixes usually results in continued repeat failures and a negative impact on organizational performance.
2. Focus on the right incidents
You can't investigate everything that goes wrong. Look for incidents with high learning value where you can learn something that will allow you to make significant positive impacts on organizational performance. These usually include the following three categories: high consequence incidents, near misses to high consequence incidents and chronic lower consequence incidents. Most organizations focus investigations on the first category and largely ignore the last two categories of incidents.
3. Get started right away
The longer it takes to get started, the harder it is to do the job right. Streamline the incident selection and personnel assignment process so that the investigation can get started immediately.
4. Get the right people involved in the investigation
Select personnel that have RCA training and the background to uncover the performance gaps that caused the incident.
5. Get the data you need
Most RCA teams don't get enough data. Data gathering is difficult and time consuming. Teams often take short cuts and only collect enough data to support their hypothesis. Unfortunately, the rest of the RCA process is ineffective if complete data are not collected.
"The most effective recommendations from an RCA are typically long-term in nature."
6. Use standard techniques for data analysis
There are many data analysis tools available including timelines, logic trees, logic tables and checklists. Each technique has its own advantages and disadvantages; none is perfect. Pick one or two and use them for every incident. Don't allow the use of other tools.
7. Require the use of a technique that identifies underlying causes
The better analysis tools guide the RCA team toward the underlying root causes. Each method has advantages and disadvantages in terms of effort required versus thoroughness and consistency. Choose one technique and require its use for every analysis. This should allow your organization to trend root causes.
8. Get management buy-in for the recommendations
Management doesn't always accept the team's recommendations, frequently due to a lack of communication. Provide management with a summary of the incident that highlights the performance gaps, or differences between what should have happened and what did happen. The performance gaps should address what occurred out in the field (the causal factors) and in the support organizations (the root causes). Show how the recommendations address the performance gaps (causal factors to root causes to recommendations). Use a standard, 3-column form showing the causal factors, root causes and recommendations to facilitate communication so that managers will understand why the team recommended what they did.
9. Track recommendations to completion
The most effective recommendations from an RCA are typically long-term in nature. Inevitably they will be pushed aside if no one tracks their progress or holds the responsible individuals accountable. A database that facilitates frequent status updates and communications with personnel is the only effective way to accomplish this goal.
10. Look for long-term trends
Most organizations needlessly tolerate inefficiencies and losses in their processes. The same failures occur often, but they are viewed as "part of the process" and "just the way things are" when in fact simple fixes can be applied to reduce the frequency and impact of these failures. Use work requests, production data and inventory records to help identify these chronic problems so that they may never be reported as incidents.
Our safety leaders understand how to manage high-consequence scenarios. Learn more about our response and experience handling Incident Investigation and RCA.