Insight
Peeking Down the Pipe: How EAM Fuels Tomorrow's Oil and Gas Industry
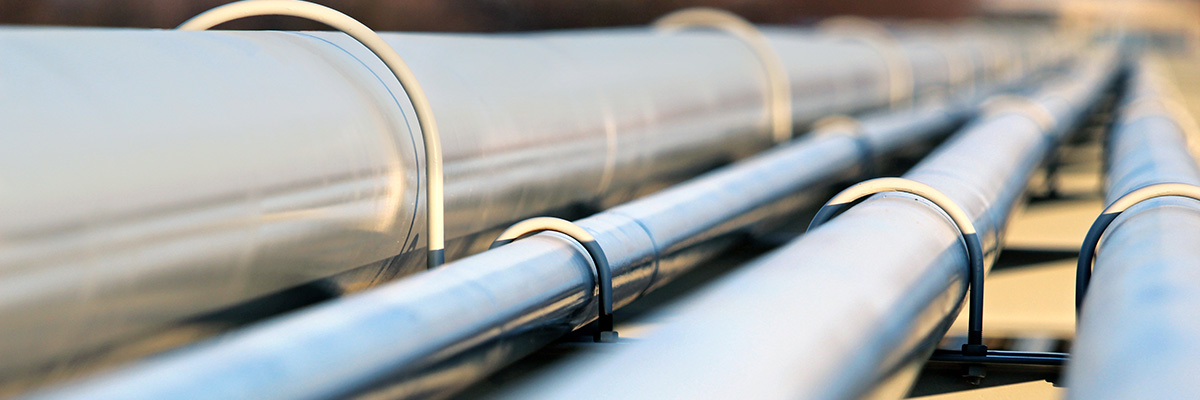
Hardly anything operates without energy today, and oil and gas companies comprise the largest share of consumed energy resources in the country across all sectors: a combined 62 percent, according to the US Energy Information Administration.
Currently, demand for high-functioning assets and uninterrupted uptime are common across many industries, but for oil and gas, the stress of continuous operations can be far greater than in other lines of work. The breadth of oil and gas production, from extraction to sale, may involve disparate facilities and a diverse logistical network, all of which rely on the performance of industrial assets. Utilizing an enterprise asset management (EAM) plan through proactive maintenance solutions affords businesses the opportunity to interact intelligently with all of their assets along a supply chain, access and analyze deficiencies and preempt issues or failures before they tamper with production.
Today's market turbulence in the oil and gas industry could be a bellwether for emerging changes to how oil and gas companies produce, which could, in turn, alter asset management strategies moving forward. As these industries look toward the future, what trends will push businesses to adopt proactive maintenance as a means of enhancing EAM?
3 Trends Impacting EAM
1. Production increases into the next decade
As US oil production and cheaper domestic gas from unconventional resource development become more attractive to international buyers, production could increase to meet growing demand abroad. This would place a particular strain on oil and gas transportation assets, such as pipelines and railcars, moving products to coastal ports. North America's abundant shale gas resources also will increase pipeline usage for power generation as the power market sector continues to evolve.
Reliability-based maintenance raises up asset performance as the catalyst for repairs and upkeep, preserving the engine of production by helping to ensure all relevant machinery functions as intended.
2. Data-intensive assets necessitate smarter production and protection
Oil and gas companies aren't just rich in natural resources, but also data. Communication and transparency along the supply chain both help businesses understand every facet of the extraction and production cycle, as well as the economic factors affecting point-of-sale revenue streams.
As assets become "smarter" and more capital-intensive, the threat of not maintaining them properly grows. A connected supply chain can still be susceptible to small operational errors. Similar to issues when facing heightened demand, asset modernization forces businesses to evolve toward data-heavy processes, compounding costs when deficiencies, failures or other downtime events occur. Proactive maintenance plans can oversee all components of a given asset, from its physical properties to the digital offerings it transmits, securing data that keeps things pumping.
3. EAM as insurance against environmental risks
As is the case in all industries charged with handling hazardous chemicals and large-scale industrial equipment, operations must adhere to strict safety guidelines to prevent disasters. To that end, proactive maintenance acts as a preemptive measure against adverse environmental impact, as well as the expenses tied to such an occurrence.
The total cost of downtime in the global process industry can be enormous--many billions annually. That said, when it comes to oil and gas production and transportation, downtime may be the least of a company's concerns. Spills not only result in penalties from regulatory bodies, possible litigation and expensive cleanup initiatives, but also a tarnished reputation in the eyes of environmentally conscious consumers, something businesses may not ever recover no matter how much money they spend attempting to do so. Apart from emergency situations, ongoing compliance concerns can be just as damaging to a brand.
Asset failures contributing to these serious ecological issues might be avoided with a comprehensive proactive maintenance plan and more thorough asset management strategies in place.
Staying Ahead with Proactive Maintenance
Though hindsight is always 20/20, oil and gas companies that understand the liabilities they undertake working in their industry should turn to reliability-based management to safeguard their operations and much more. After all, real EAM can be a valuable tool in prevention of costly catastrophes, but its adoption involves a restructuring of commercial and industrial philosophies about asset performance – not only what it means for business but to consumers, the environment and everybody watching the oil and gas industry.
See how we assist the Oil, Gas and Chemical market and learn more about Asset Management.