Insight
How Process Safety Management With Mechanical Integrity Drives Operational Excellence
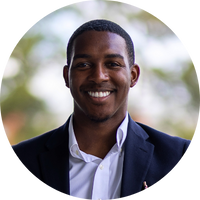
Javier Castro
Director, Business Development
Every journey begins with understanding where you are and where you want to go. And for any chemical processing plant, process safety management is an important journey that can deliver significant benefits. Yet all too often, organizations are viewing risk from a compliance perspective.
According to Javier Castro, Director, Business Development at ABS Consulting, the journey towards operational excellence begins with a change in mindset. Shifting from a compliance perspective to seeing the true value and benefit of process safety through mechanical integrity programs can help take organizations from firefighting to knowledge-based, data-driven asset management decisions.
Understanding Your Chemical Processing Operations
The ideal scenario for any business involved with chemical processing is to know what is happening within their automated operations. Critical to this approach is the use of technology to first help better understand how equipment is operating, which can then help to establish a knowledge-based preventative approach to critical operating equipment.
The goal is to reduce unplanned downtime as it is expensive, can have a major impact on an organization's operational efficiency and ultimately, can negatively impact its bottom line.
Taking a data-driven approach to process safety and maintenance can help identify any ‘bad actors’ within the business, spotting where issues lie so they can focus attention on addressing real problems and not every problem.
Process safety is built on effective resource management, and central to this is computerized maintenance and management systems (CMMS). A lot of the information needed to make better-informed decisions is available to organizations today, but experience shows that while they may have the information, the vast majority are either not using it, or do not know how to best use it to their benefit to increase the reliability and safety continuum.
From a Risk Analysis perspective, many organizations currently have no systems or processes in place to collate, review and determine what their data is telling them and what decisions and actions they should therefore take. It’s the equivalent of driving a car with none of the warning lights working – it’s only a matter of time before something goes wrong.
And most times this is exactly what happens, resulting in firefighting – with maintenance teams reacting to equipment problems only when they arise. Because this is the way they have always operated, they often don’t realize how reactive they are, or when they do occur, measure how that approach impacts the bottom-line perspective.
The more unplanned work you are forced to react to, the heavier the cost incurred. This is the most inefficient and the least safe way of operating, as an organization is not planning its work; instead, the machine is dictating what it is doing.
So, the question is - where to start? We should start by setting metrics – using the existing data on hand to establish a baseline picture, utilizing all the data sets to see:
- Where you are
- What information you have
- What it is telling you
- What it is identifying
Everything revolves around a continual improvement wheel by utilizing technology and data to help us better understand how equipment is operating, and by doing so, start to establish a knowledge-based preventative approach to operating equipment. We want to be more efficient and reduce critical costs such as non-contract labor, and in doing so improve safety, reliability and efficiency.
Digital Transformation
Through effective data management, Digital Transformation is enabling organizations to make better decisions around their risks and to determine where to place their focus from a maintenance and safety perspective.
You cannot move up the maturity continuum if you are not planning and managing your maintenance and repair schedules. The goal is for preventative maintenance to identify, mitigate and dictate actions. You want to have a maintenance action before there is a functional failure. When we are not identifying and mitigating then the machine will ultimately suffer a functional failure.
What we are trying to achieve is a risk-based approach of using data to look for the right things in the right place at the right time. If you cannot do this, then you cannot identify your risks properly.
Identifying risk enables an organization to place its resources in the best places. By taking a technical and systematic approach to identifying and measuring the risks, organizations can start to move forward, away from the firefighting phase.
Through digital transformation, organizations can build robust process safety and mechanical integrity programs by embracing real time data, predictive models, data-driven tools and tools that can assess asset life expectancy.
It helps move an organization from ‘we think’ or ‘we hope’ to ‘we know’ – helping to enable time, effort and money to be focused precisely where it needs to be.
Key Steps to Operational Excellence
There are 4 key phases to achieving operational excellence – Mitigation, Compliance, Risk-Based and Enterprise. Organizations will have to work their way through each phase in turn and will not be able to skip a phase.
1. Mitigation Phase
In this stage many organizations are in firefighting mode. They will have a repair-based asset management approach where asset failures are expected and accepted. There can be a ‘we hope it doesn’t leak’ approach to assets.
In this phase your people are ‘fire-fighting heroes’, reacting to the fact there is limited process development. Systems often revolve around CMMS Repair Work Orders and there is limited use of technology, and limited inspection and NDE.
Asset performance usually looks like having to deal with unexpected failures with increasing frequency and severity. In this scenario a lot of assets within an organization are operating to failure.
2. Compliance Phase
The compliance phase is a time-based asset management phase where all potential failures are treated equally. This planned maintenance stage is about trying to prevent failure.
Organization's people will include Inspectors and NDE SMEs, and its processes will include Inspection and NDE Requirements and Procedures. Systems will include CMMS I&T Events/Hard Copy Report Files, and technology will include visual Inspection and Basic NDE.
From an asset performance perspective, an organization can expect a reduced number and severity of failures, with 5-10% reduction of unexpected failure costs, increased I&T and planned downtime costs.
3. Risk-Based Optimization Phase
In this phase organizations will be more predictive in their monitoring, taking a technical-based approach to asset management. Potential failures are prioritized based on risk. At this stage an organization understands damage mechanisms and risks, and focuses on an identified priority.
Its people will include Corrosion, Inspection/NDE, Process, and Operation SMEs, using technical work processes and systems including IDMS with RBI and CML Management, and technology including DMA, RBI and Advanced NDE.
Asset performance should include few unexpected failures with significant impact due to risks being managed. Unexpected failure costs can be further reduced by 30-35% with lower I&T and planned downtime costs.
4. Enterprise Level Phase
This stage uses data to make decisions on business-based asset management. Potential failures are proactively managed to optimize ownership cost. They are optimizing assets costs and life.
The organization will have a team of Technical and Business SMEs, using Integrated Technical and Business Work Processes through CMMS, IDMS, PI and Business Systems. Technology utilized will include metals upgrade, advanced equipment/process sensors, IOWs, data analytics and CI.
There are rare, unexpected failures, with unexpected failure costs reduced by up to 50-60% with optimized I&T costs and asset life extension.
Conclusion
There are two fundamental benefits for organizations that shift their perspective from the view of compliance to one of process safety and asset integrity:
- Preserving their right to operate – keeping regulators at bay, staying out of the news and safeguarding reputational value.
- Getting a return on investment – this is where operational excellence and integrity come in – people, investments and managing risks, including regulatory risk, process safety risk, enterprise risk and operational risk.
The benefits can be felt from the plant floor to the board room – the use of technology helps to enable positive change throughout the organization.