Insight
How CMMS Software Turns Data into Asset Reliability
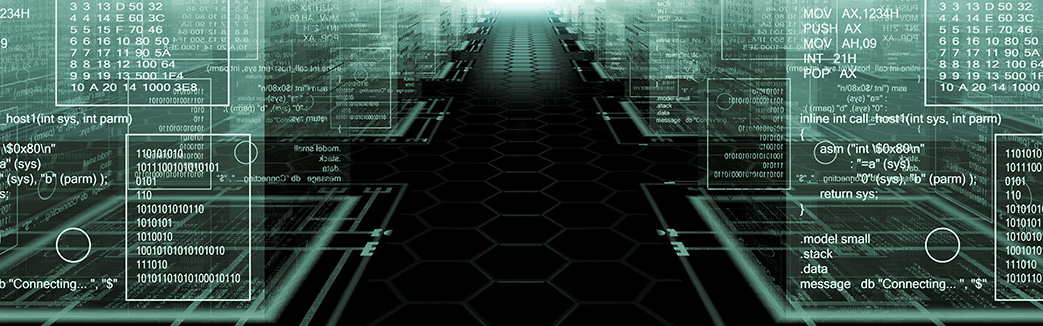
Keeping large cost-intensive assets functioning over the course of their life cycles requires much more than a tool box, especially in an age of seemingly continuous production.
As volumes increase, customers throttle up demand or new products diversify a company's offerings, manufacturers have the potential to scale up successfully. But this prosperity isn't a sure thing – asset failures, even small temporary ones, chip away at a manufacturer's operational reliability. These deficiencies can eat away at profits, perhaps more so than supervisors or managers may notice at first.
As Maintenance Technology points out, a typical outlook driving a commercial investment perspective views operational costs as a subtractive force from overall profits: Profits = Sales - Cost. While this figure is undoubtedly true, it reduces all costs – both the "necessary evils" and the beneficial expenses like Reliability Based Maintenance (RBM) – to the same variable. Doing so can cloud a plant supervisor's judgment regarding proactive maintenance programs. For the manufacturing facility focused on strictly reducing costs, a reactive maintenance program appears to be the most cost-effective. After all, not addressing repairs until equipment fails suspends spending until it's absolutely necessary. Isn't that the most efficient way to expend company resources?
"There's quite a large 'gray zone' between functional equipment and failing equipment."
Though proactive maintenance solutions call for regularly scheduled repairs to improve asset reliability – and as such, small investments throughout an asset's lifespan – this system of Enterprise Asset Management demonstrably protects manufacturers from overspending on both maintenance and across other departments. For example, there's quite a large "gray zone" between functional equipment and failing equipment. RBM not only wards off huge system-wide breakdowns, but also addresses smaller operational inefficiencies that accumulate over time. These discrepancies could compromise the quality of the products a manufacturer produces, make work more complicated for asset operators and draw out lead times, all of which end up costing manufacturers a considerable chunk of change in the process.
Additionally, manufacturers should all believe in Murphy's Law, the superstition that dictates if something can go wrong, it most certainly will. Without a proactive maintenance program in place, failures will occur. Downtime will happen when a manufacturing facility least expects it, or at the very least, when it is most inconvenient. Imagine the last time your car got a flat tire. Did it happen as you were pulling into your driveway? Most likely not. The same principle applies to asset management: Planned maintenance can minimize resource spend on repairs while running a machine to failure leaves the whole thing to chance.
CMMS Software: Managing Asset Data
A supporting component to the proactive maintenance foundation is the incorporation of computerized maintenance management system (CMMS) software, which establishes a database for all information gleaned from maintenance monitoring sensors throughout company assets. CMMS software creates a framework for how owners and users should organize this pertinent data, as well as establishing a hierarchy of interoperability as to how this data impacts disparate plant operations. From CMMS software, maintenance professionals can deduce how best to address slipping asset performance or a looming failure long before it completely opposes productivity.
Risk avoidance is one of the single greatest threats to effective asset management, according to Reliable Plant. Without accurately communicated information from an asset to its operator, operators cannot make the best decisions toward RBM.
Let's take a closer look and uncover how these datasets contribute to a more consummate proactive maintenance program fueled by reliability as much as cost-cutting.
Failure Code Analysis
Simply put, failure code analysis identifies the exact malfunctioning component maintenance professionals must focus their attentions on to effectively conclude the root cause underpinning operational inconsistency. As obvious as the benefits of this service may appear, noting the exact origin of maintenance issues can optimize RBM to its most cost-efficient state. For instance, replacing worn fan belts from time to time might be part of a proactive maintenance plan, but only if the maintenance crews can say with certainly other machinations aren't rending the fan belts. CMMS will account for all of these fan belt replacements, drawing attention to their frequency and the possibility of an external force creating stress on the component.
Mean Cost to Repair
Mean Cost to Repair (MCTR) may seem just as self-explanatory, but once again, this variable necessitates the collection of information concluding an asset's total cost of ownership (TCO). When CMMS collects MCTR data, it automates the auditing process required in every proactive maintenance plan to ensure both reliability and cost-efficiency. Decommissioned equipment doesn't just impact production, but employee assignments, warehouse logistics and potentially part replacement, as well as the administrative costs surrounding ordering and acquiring said component.
Mean Time Between Failures, Mean Time to Repair
Essentially, both Mean Time Between Failures (MTBF) and Mean Time to Repair (MTTR) are separate tiles comprising the mosaic of MCTR. That said, they're worth highlighting because of how they relate to maintenance performed on an asset rather than the asset itself.
MTBF, for starters, creates something of an experimental control group in a maintenance scenario. This variable asks the question, "How long will it take a particular repair issue to cause a complete system failure?" Not only does this information give maintenance professionals a well-rounded perspective on whether a repair is necessary as soon as possible, but it also allows repair teams to better manage future maintenance. A malfunctioning component with a high MTBF allows maintenance crews to weigh the immediacy of repair against the timeliness of a scheduled shutdown.
"Mean Time to Repair allows repair teams to better manage future maintenance."
In a similar vein, MTTR accounts for both the average repair times for individual components, as well as the frequency of repairs over a chosen duration of time. Ultimately, this factor provides maintenance professionals with an objective view of how often repairs on certain components crop up and insight into TCO as it relates to the length of a single repair cycle. Moreover, manufacturers can use MTTR to scrutinize how well assets detect and report their own reliability issues. If MTTR doesn't appear representative of the extent of the damage maintenance professionals uncover, this could push manufacturers to invest in better sensors to promote a more comprehensive proactive maintenance plan.
Cost-efficiency and reliability aren't mutually exclusive concepts. EAM powered by RBM can work wonders with small operational investments. Why wait until an absolute emergency dictates how much manufacturers will be forced to pour into repairs? CMMS software and their data streams maximize productivity as they hone spending to promote a more intelligent approach to asset management.
Interested in applying our EAM approach? Learn more about Asset Management.